PLANTS
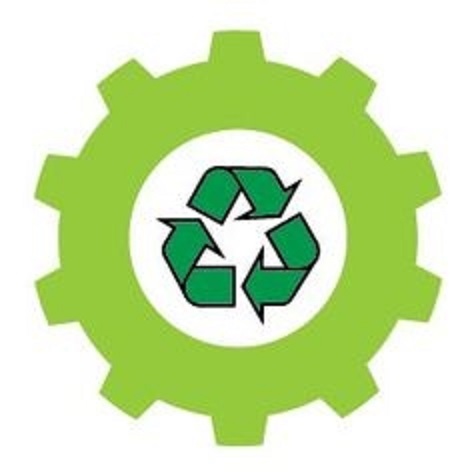
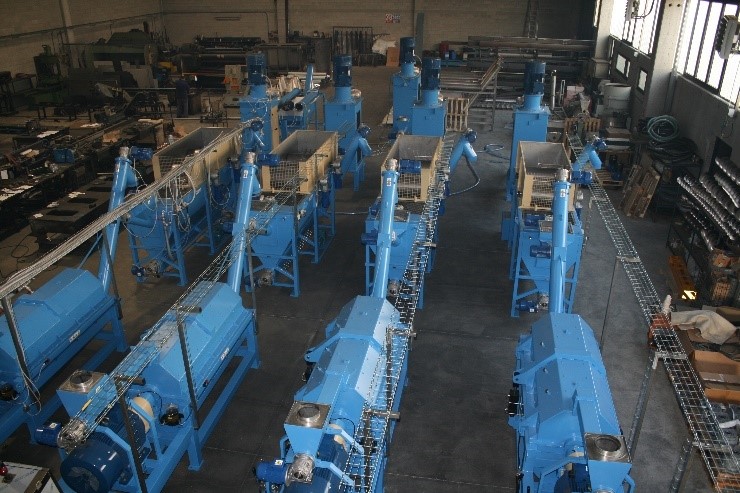
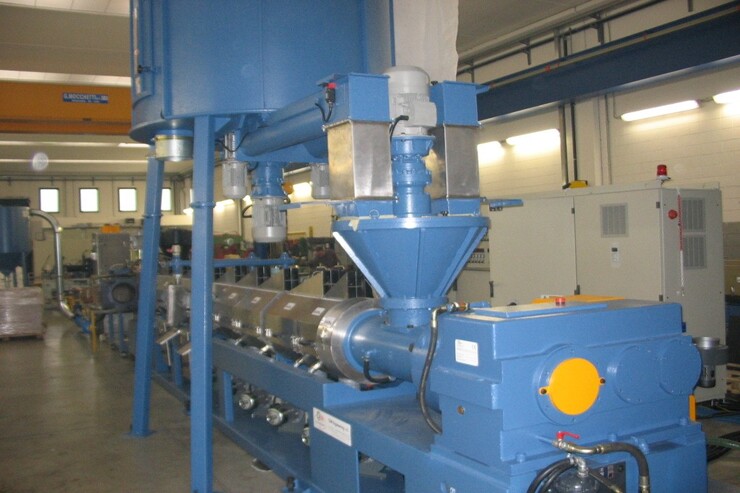
Among the range of products, we can offer complete recycling plants with single-screw extrusion of exclusive production by CDM Engineering Srl – OMP Prealpina, such as:
– LDPE/HDPE/PP/PS/EPS film extruders
– LDPE/HDPE/PP/PS/EPS heavy regrind extruders
SINGLE SCREW EXTRUDERS
- With single or double degassing
- Granulation with die face or strand cutting system
- Made with barrel ranging from Ø 35 mm to Ø 180 mm.
- Output from 20 to 1.400kg/h
DEGASSING SINGLE SCREW EXTRUDERS
- The degassing extruders have been designed to increase the degassing efficiency of the extrusion plant. They are connected in series to the main primary extruder through the appropriate connecting neck.
- made with barrels from Ø 160 to Ø 250 mm
TWIN-SCREW EXTRUDERS
- Twin-screw extruders stand out from single-screw ones for their high performance in terms of feeding, mixing, plasticizing, venting, reaction, and vacuum discharge.
- made with barrels from Ø70 to Ø170mm
- output from 300 to 3000kg/h
SINGLE SCREW EXTRUDER
- with single or double degassing
- granulation with die face or strand cutting system
- made with barrel ranging from Ø 35 to Ø 180 mm
- output from 20 to 1400kg/h
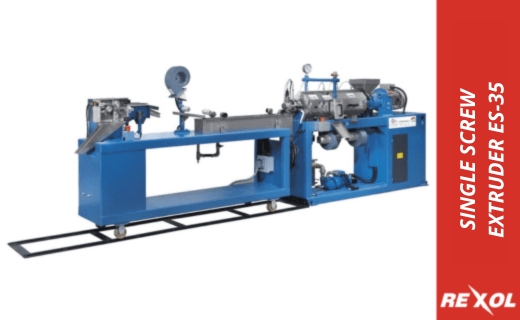
ES 35
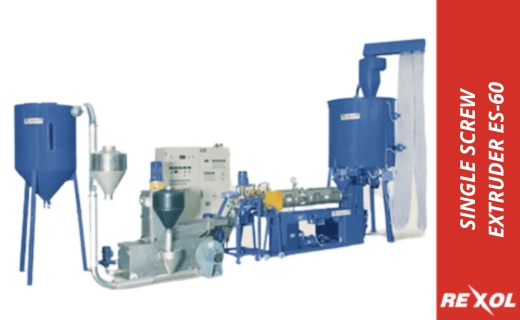
ES 60
Complete line, suitable for LDPE/HDPE/PP film
Output: 110 – 150 kg/h.
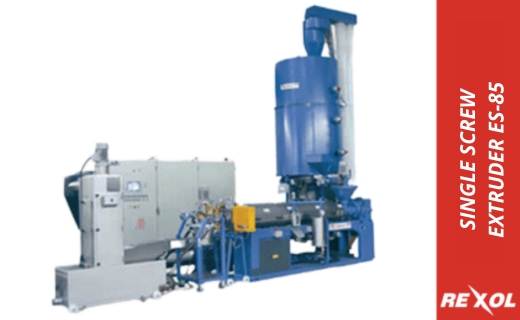
ES 85
Complete line, suitable for LDPE/HDPE/PP/EPS/EPE film
Output: 250 – 300 kg/h.
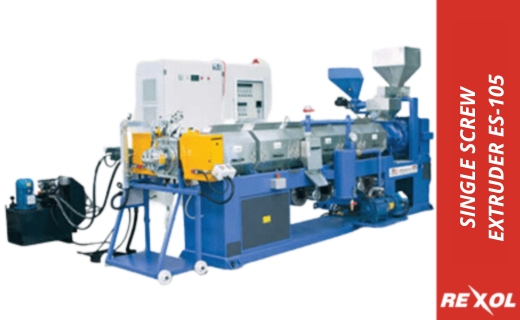
ES 105
Extruder with screenchanger and strand die, suitable for LDPE/HDPE/PP/PS/ABS/PA regrind.
Produzione: 300 – 500 kg/h.
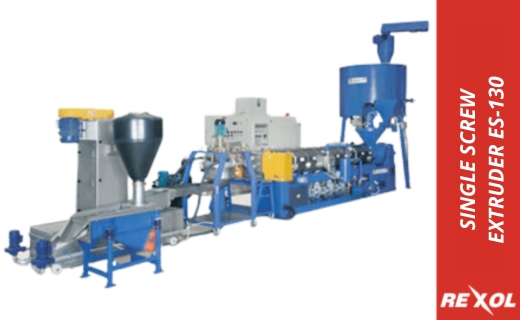
ES 130
Complete line, suitable for LDPE/HDPE/PP/EPS/EPE film.
Output: 500 – 600 kg/h.
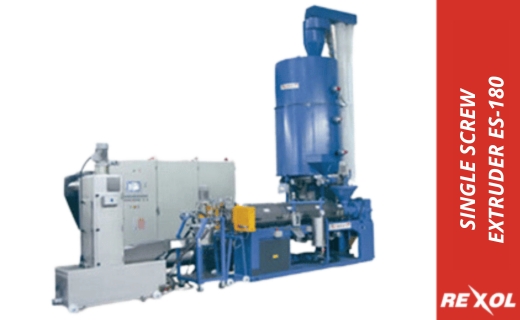
ES 180
Complete line, suitable for LDPE/HDPE/PP/EPS/EPE film
Output: 900 – 1100 kg/h.
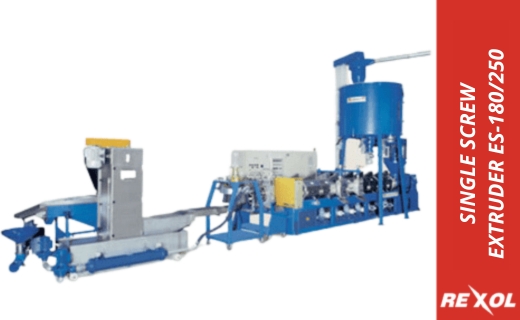
ES 180 -> ES 250
Complete line, suitable for FILM LDPE/HDPE/PP/EPS/EPE
Output: 900 – 1100 kg/h.
DEGASSING SINGLE SCREW EXTRUDERS
The degassing extruders have been designed to increase the degassing efficiency of
extrusion plants. They are connected in series to the main primary extruder through the appropriate connecting neck.
The three key characteristics that distinguish these extruders are:
- A much larger degassing zone compared to the main extruder
- Larger screw diameter
- Low operating speed
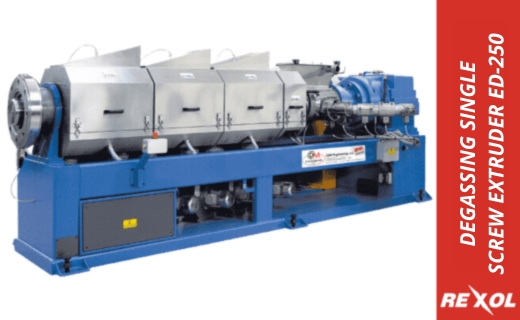
ED 250
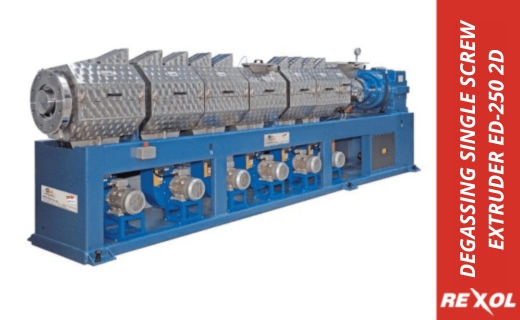
ED 250 2D
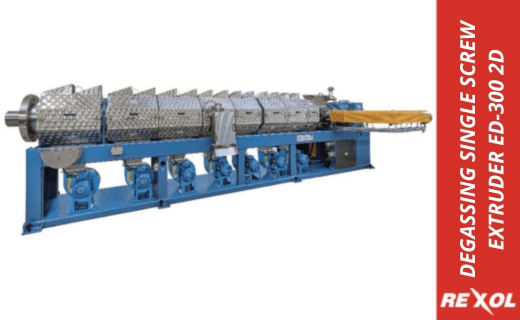
ED 300 2D
TWIN -SCREW EXTRUDERS
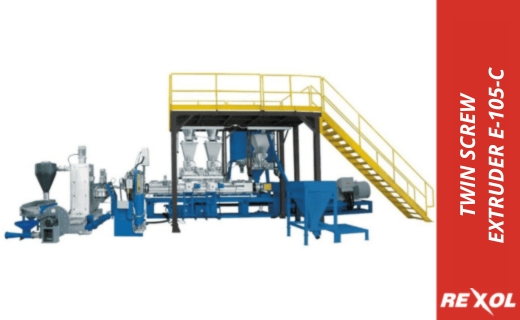
E 105 C
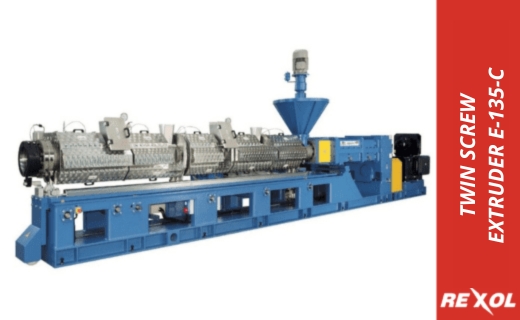
E 135 C
EXTRUSION EQUIPMENT
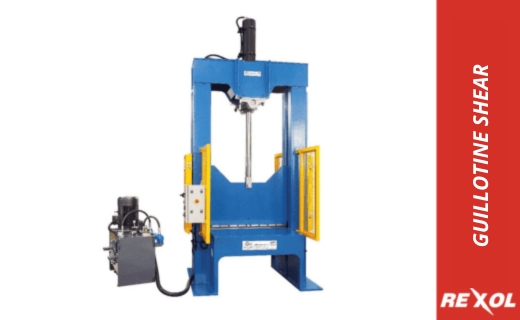
GUILLOTINE SHEAR
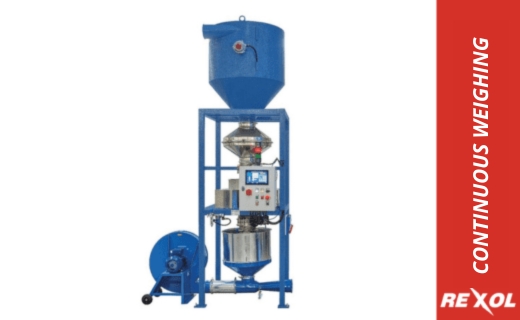
CONTINUOUS WEIGHING
Among the range of products, we can offer, in collaboration with REG-MAC Srl, washing plants and machines such as:
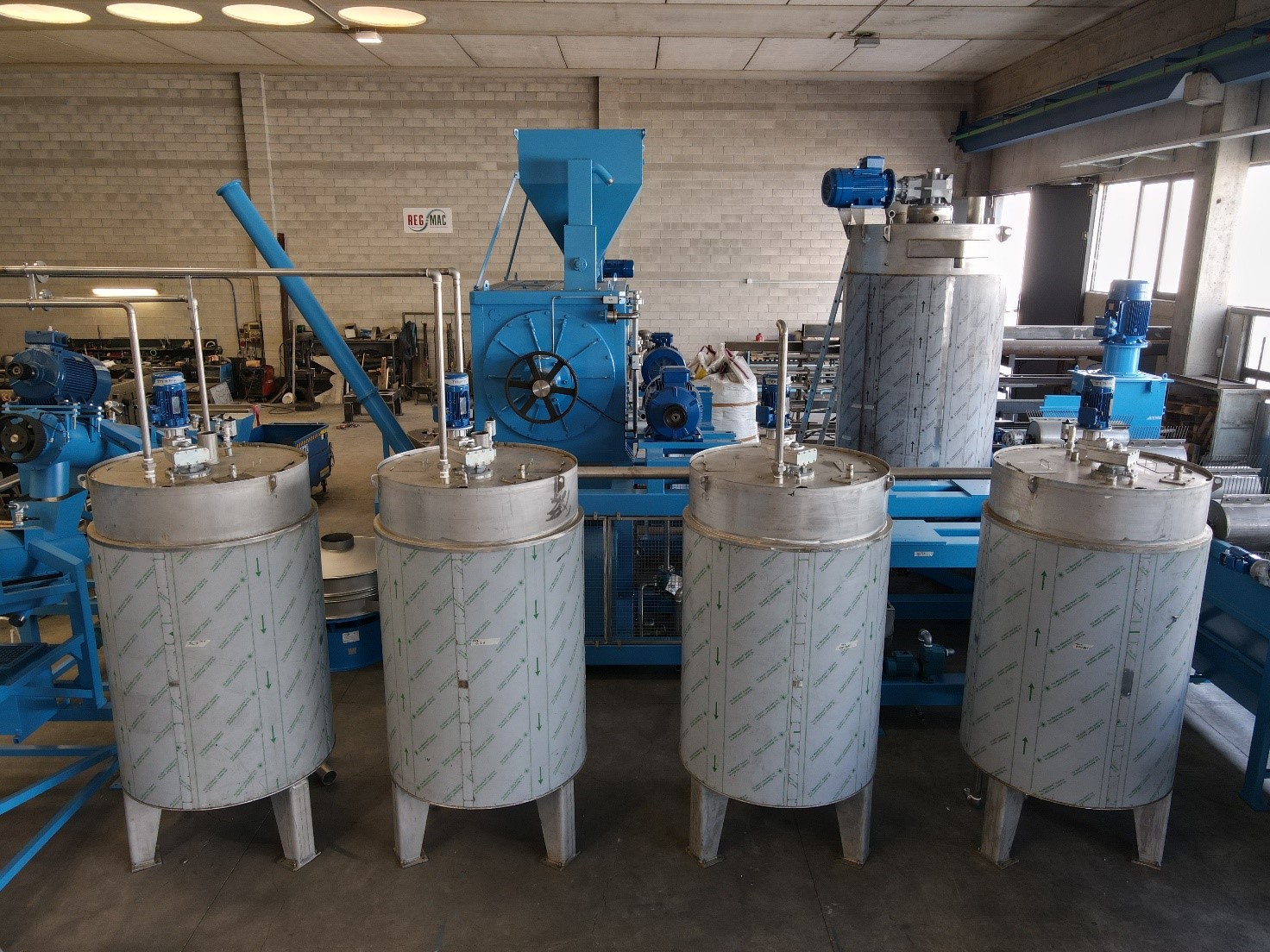
COLD WASH
Ideal for cold washing of rigid flakes of LDPE, HDPE, PP, PS, or PVC with a medium to high degree of contamination.
HOT WASH
Ideal for intensive hot washing of PET and HDPE flakes. The entire process is customized according to the final use of the washed flakes for fibres, for thermoforming sheets, or for blow moulding bottles.
WASHING MACHINES
Individual machines available for separate sale for the recycling of post-production and post-consumer thermoplastic waste.
COLD WASH PLANTS
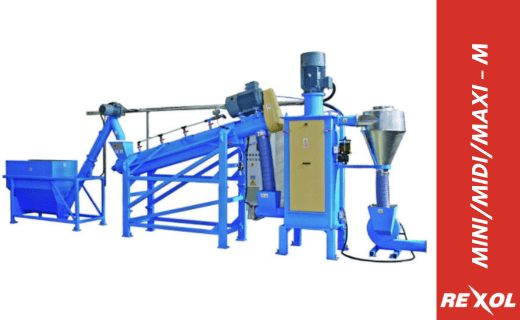
MINI/MIDI/MAXI – M
For input capacities ranging from 300 to 1500 kg/h of slightly contaminated materials
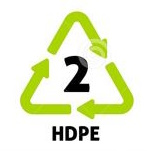
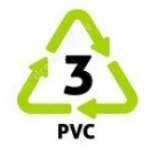
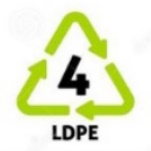
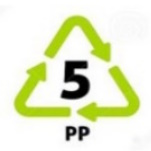
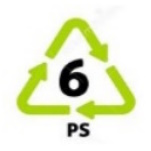
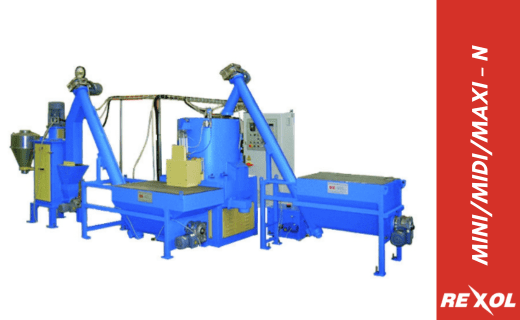
MINI/MIDI/MAXI – N
For input capacities ranging from 300 to 1500 kg/h of highly contaminated materials.
High-friction washing, for the removal of the most stubborn impurities, is performed with adjustable cycles set on the control panel.
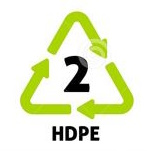
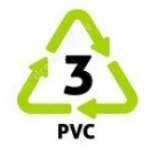
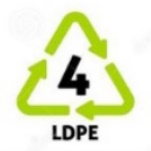
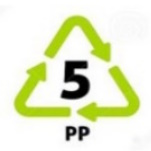
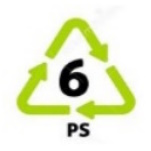
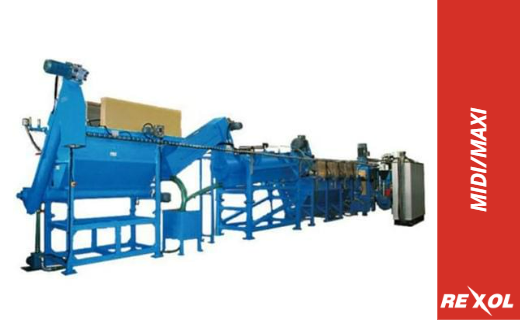
MIDI/MAXI
For input capacities ranging from 500 to 1500 kg/h of moderately or highly contaminated materials.
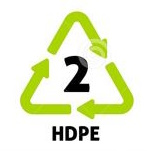
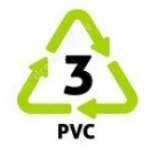
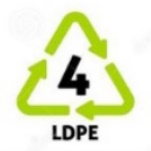
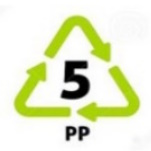
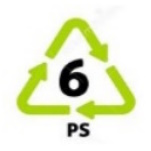
HOT WASH PLANTS
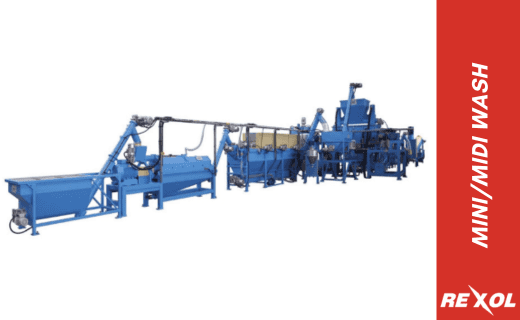
MINI/MIDI WASH
For input capacities ranging from 600-800 kg/h of slightly contaminated flakes.
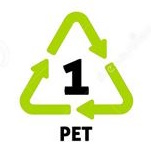
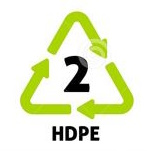
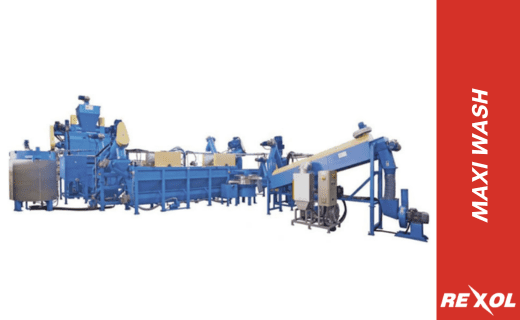
MAXI WASH
For input capacities ranging from 1000-1500 kg/h of highly contaminated flakes.
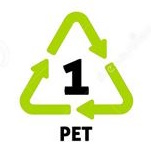
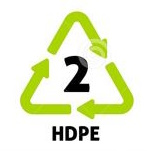
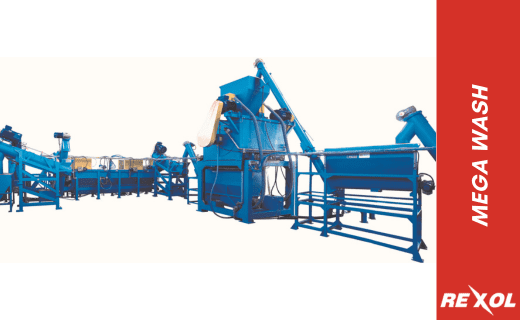
MEGA WASH
For input capacities ranging from 2000-2500 kg/h of highly contaminated flakes.
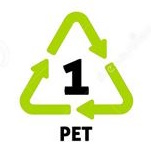
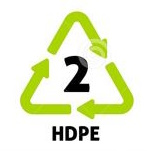
WASHING MACHINES
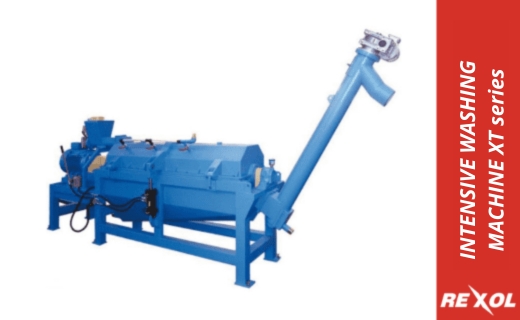
INTENSIVE WASHING MACHINE XT series
Designed for intensive washing of rigid or flexible flakes with a high level of contamination.
It is available in 3 sizes with production capacities ranging from 500 to 2,500 kg/h.
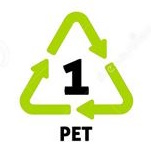
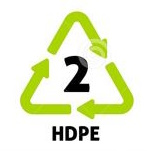
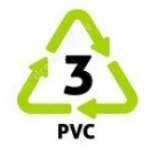
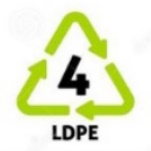
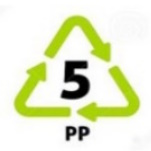
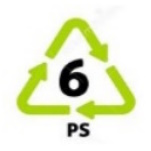
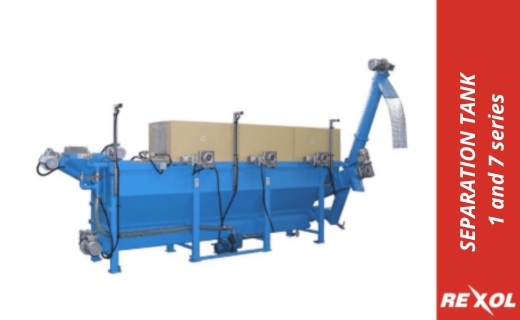
SEPARATION TANK 1 and 7 series
The separation tank performs gravity separation of non-homogeneous regrind material. The extraction of the light and heavy fraction is carried out through separately operated augers.
The separation tank is available in 4 standard sizes with treatment capacities ranging from 300 to 2.500 kg/h.
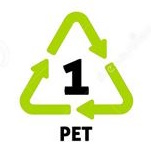
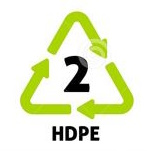
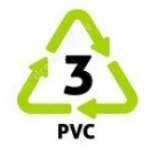
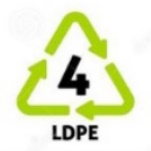
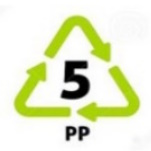
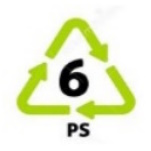
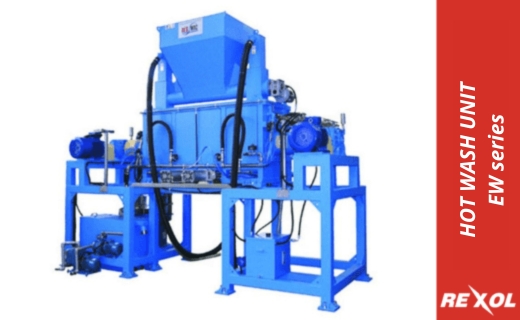
HOT WASH UNIT – EW series
The HOT WASH unit has been designed for removing adhesive, grease, and oily residues from the surface of the ground material. Intensive washing is carried out using hot water and detergents in the tank, and through continuous friction and agitation, it also removes the most stubborn particles.
The HOT WASH unit is available in 4 standard sizes with treatment capacities ranging from 600 to 2.500 kg/h.
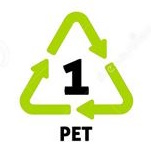
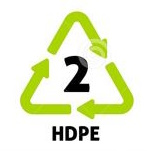
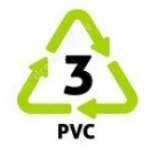
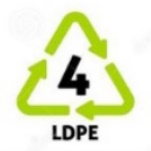
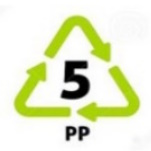
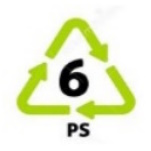
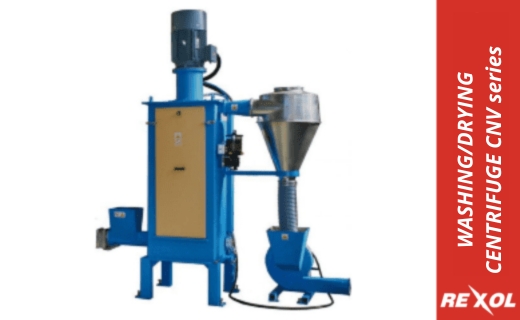
WASHING/DRYING CENTRIFUGE CNV series
Designed for washing or drying rigid or flexible flakes with low contamination levels.
It is available in 4 versions with treatment capacities ranging from 300 to 1.500 kg/h.
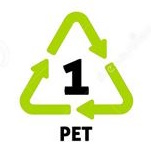
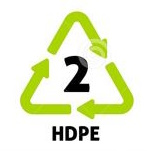
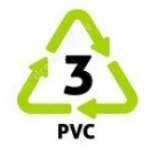
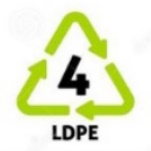
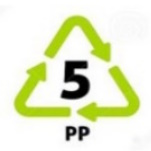
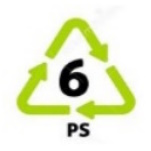
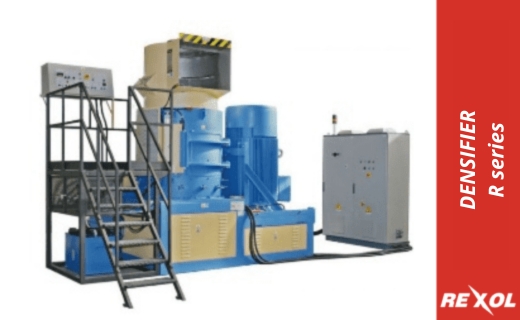
DENSIFIER, R series
This machine has been designed to increase the density of clean recycled thermoplastic material, ensuring color and specific weight uniformity. It is particularly suitable for processing flexible packaging and tough fibers (PET and PP).
Available in 3 models with agglomeration capacity ranging from 150 to 1,400 kg/h.
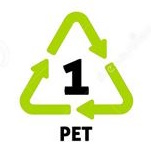
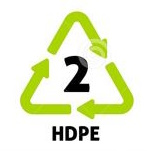
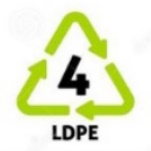
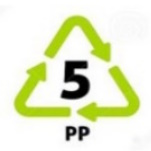
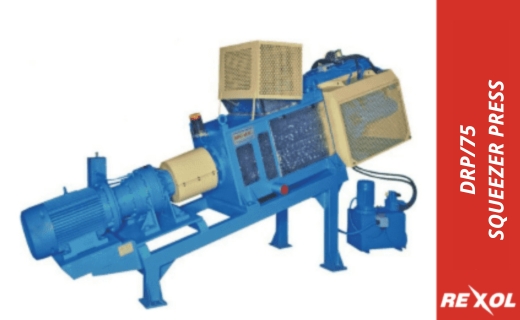
DRP/75 SQUEEZER PRESS
The press has been designed for continuous squeezing of wet flakes of thermoplastic film from washing to significantly reduce the final moisture content of the material.
The counterpressure value is constantly self-regulated by an adjustable hydraulic circuit, even during processing.
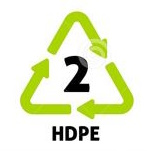
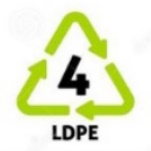
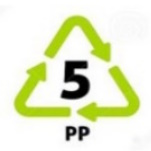
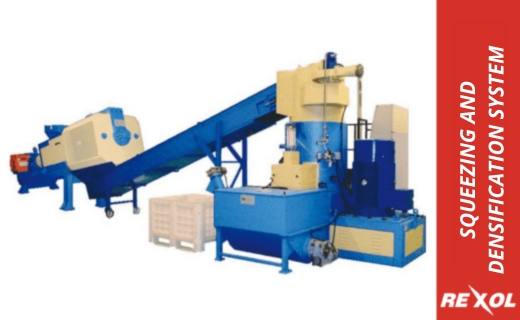
SQUEEZING AND DENSIFICATION SYSTEM
ES 35
The standard line setup:
- Extruder Ø 35 mm L/D 35 with single degassing, reducer, cylinder and screw in nitrided steel
- Vacuum system for degassing
- Main motor 7.5 kW alternating current controlled by inverter
- Electric panel for temperature control
ES 60
The standard line setup:
- Flakes silo (2; 4 m³)
- Dosing auger for flakes silo
- Variable speed crammer feeder
- Extruder Ø 60 mm L/D 35 with single vent, gearbox, nitrated barrel and nitrated screw
- Vacuum pump group for vent with water collection tank
- Inverter controlled A.C. main motor, 45 kW
- Electric control cabinet
Outuput kg/h (LDPE) | A.C. motor power kW | Filtration area Ømm |
110 – 150 | 45 | 115 – 130 |
ES 85
The standard line setup:
- Flakes silo (4 m³)
- Dosing auger for flakes silo
- Variable speed crammer feeder
- Extruder Ø 85 mm L/D 35 with single or double vent, gearbox, bimetallic barrel and stellited screw
- Vacuum pump group for vent with water collection tank
- nverter controlled A.C. main motor, 98 kW
Output kg/h (LDPE) | A.C. Motor power kW | Filtration area Ømm |
240 – 320 | 98 | 145 – 170 |
ES 105
The standard line setup:
- Flakes silo (4; 7 m³)
- Dosing auger for flakes silo
- Variable speed crammer feeder
- Extruder Ø 105 mm L/D 35 with single or double vent, gearbox, bimetallic barrel and stellited screw
- Vacuum pump group for vent with water collection tank
- Inverter controlled A.C. main motor, 132 kW
Output kg/h (LDPE) | A.C. Motor power kW | Filtration area Ømm |
380 – 450 | 132 | 190 – 230 |
ES 130
The standard line setup:
- Flakes silo (7; 10 m³)
- Dosing auger for flakes silo
- Variable speed crammer feeder
- Extruder Ø 130 mm L/D 35 with single or double vent, gearbox, bimetallic barrel and stellited screw
- Vacuum pump group for vent with water collection tank
- Inverter controlled A.C. main motor, 280 kW
- Electric control cabinet
Output kg/h (LDPE) | A.C. Motor power kW | Filtration area Ømm |
550 – 800 | 280 | 230 – 300 |
ES 180
The standard line setup:
- Flakes silo (7; 10 m³)
- Dosing auger for flakes silo
- Variable speed crammer feeder
- Extruder Ø 180 mm L/D 35 with double vent, gearbox, bimetallic barrel and stellited screw
- Vacuum pump group for vent with water collection tank
- Inverter controlled A.C. main motor, 395 kW
- Electric control cabinet
Output kg/h (LDPE) | A.C. Motor power kW | Filtration area Ømm |
1000 – 1400 | 395 | 300 – 400 |
ES 180 -> ES 250
The standard line setup:
- Flakes silo (7; 10 m³)
- Dosing auger for flakes silo
- Variable speed crammer feeder
- 1. Extruder Ø 180 mm L/D 35 with vent, gearbox, bimetallic barrel and stellited screw
- 2. Extruder Ø 250 L/D 12 with vent, gearbox, bimetallic barrel and stellited screw
- Vacuum pump group for vent with water collection tank
- Inverter controlled A.C. main motor, 395 kW
- Electric control cabinet
Connexion | Output kg/h (LDPE) | A.C. Motor power kW | Filtration area Ømm |
ES 130 -> ES 220 | 400 – 600 | 280 > 200 | 230 – 300 |
ES 180 -> ES 250 | 900 – 1100 | 395 > 205 | 300 – 400 |
ES 180 -> ES 300 | 100 – 1400 | 395 > 280 | 300 – 400 |
ED 250 – ED 250 2D – ED 300 2D
Extruder | Output kg/h (LDPE) | A.C. Motor power kW | Filtration area Ømm |
ED 250 | 1500 | 200 | 230 – 300 |
ES 250 2D | 1500 | 200 | 300 – 400 |
ES 300 2D | 2800 | 280 | 300 – 400 |
E 105 C – E 135 C
Extruder | Output kg/h (LDPE) | A.C. Motor power kW |
E 105 C | 1500 | 395 |
ES 135 C | 3000 | 640 |